Stress in engineering, machine design is the amount of force acting on a unit area. In other words, stress is the force divided by area. There are many types of stress in engineering.
Moreover, the force acting on the unit area is not used for calculating bending and torsional stresses. Therefore, it’s a special case.
![where
T
F
A
shear stress [Pa]
applied force [N]
cross sectional area
2
m](https://mechcollege.com/wp-content/uploads/2021/06/image-71.png)
Stress is expressed in a few symbols, and the most popular usage is the lower case Greek letter Sigma – σ. However, in many engineering textbooks, it’s presented as lower case Greek letter Tau – τ.
In this article, you’ll learn about 5 different types of stresses that act on machine elements/ parts.
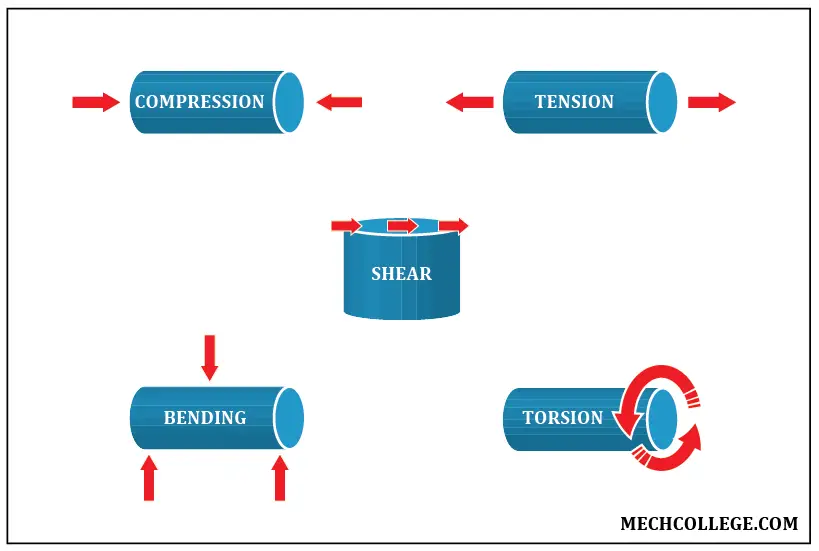
Tensile Stress
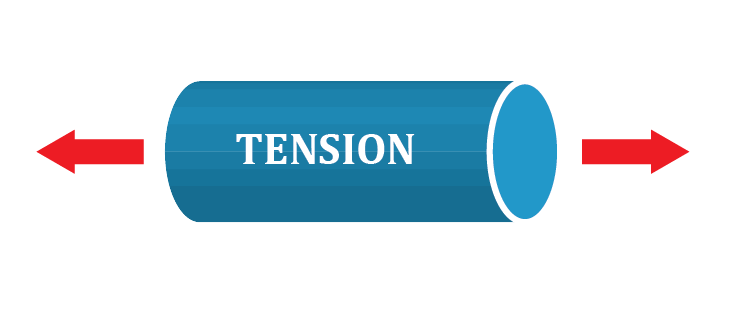
Tensile stress is the resistance of a substance to tear into pieces.
If we pull a cylindrical item in two sides, the stress equals the amount of force applied, divided by the area of the base of the cylinder.
When we measure the stress, along with the change in length (strain), we may see few visible variations in stress. And this curve is called a stress-strain curve.
These visible variations in the stress, are recognized as the strength of points. Strength is a point where anything of interest happens. In other words, it’s the ability of a substance to absorb stress.
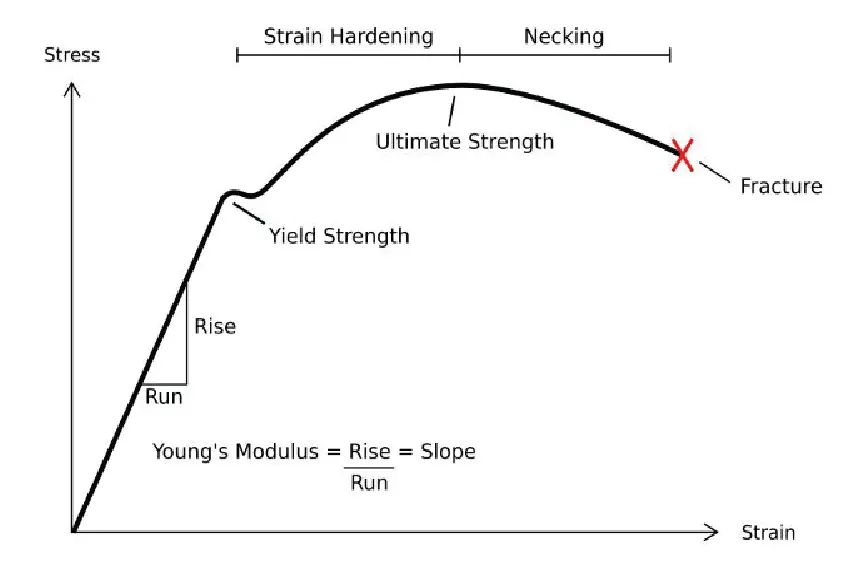
In the stress-strain curve, we can see three stresses.
- Yield Strength
- Ultimate Tensile Strength
- Fracture Strength
Compressive stress
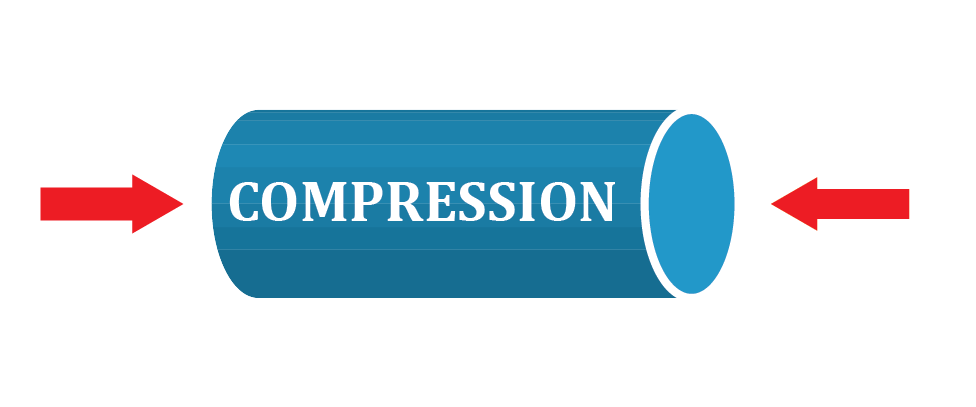
Compressive stress is the resistance of a material compress.
For example, if you push a cylindrical item in two opposed directions, the compressive stress equals the amount of force exerted divided by the area of the base of the cylinder.
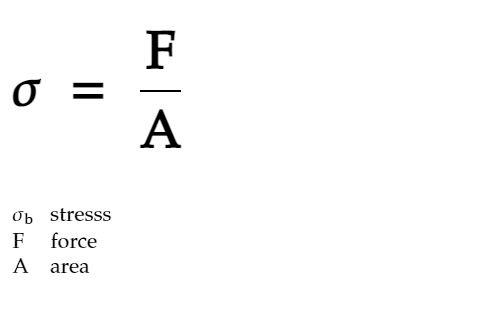
Let’s consider the image below. In this image, the metallic specimen is subjected to a resultant force acting along the axis of the cylinder. And the force is acting on a cross-sectional area perpendicular to the base.
Let’s examine the above image. If we consider it as a metallic specimen, and it’s exposed to a resultant force operating along the axis of the cylinder. And then the force is exerted on a cross-sectional area perpendicular to the base. That’s what compressive stress is.
Shear stress
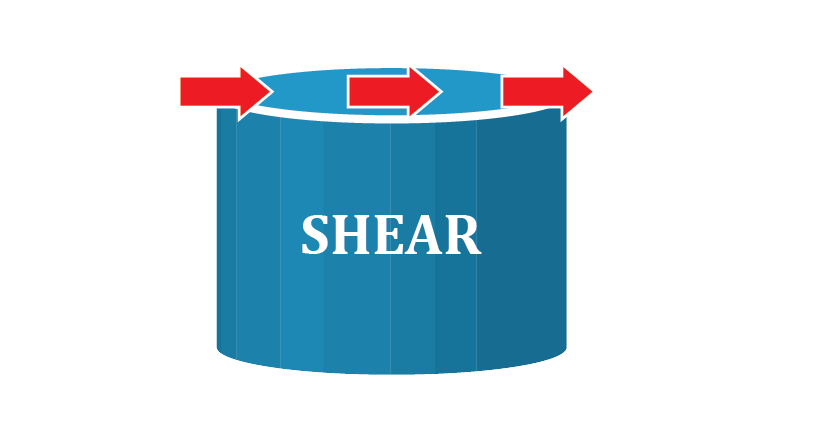
Shear stress is the resistance to deform due to perpendicular forces operating along with the surface. For example, if you attempt to push your desk both parallel and along with the direction of the desk surface, the shear stress is equal to the amount of force applied, divided by the area.
A force that is along with the surface and perpendicular to the surface is known as tangential force. So, we can say that when a body is subjected to two equal forces in opposite directions.
A force that is along with the surface and perpendicular to the surface is called tangential force. In other words, when a body is subjected to two equal and tangential forces acting on an object in opposite directions, the body tries to shear off the section. And the stress-induced is the shear stress.
Bending Stress
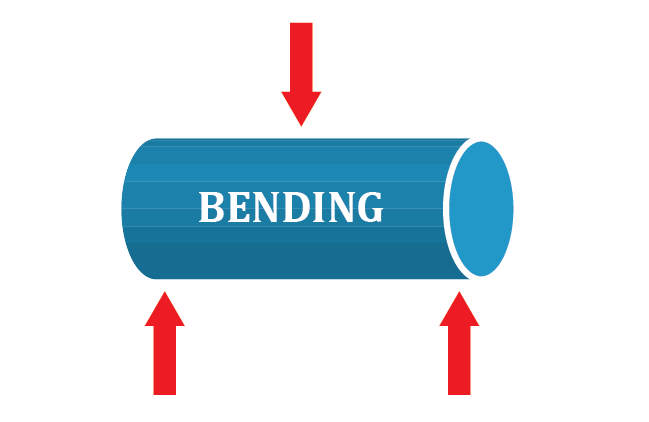
Bending stress is the resistance of an object to bend. In bending, the force is a normal load and applied at a specific spot of the object. In other words, a bending moment is a measure of the bending effect which is developed internally due to external loads.
The fundamental principle of bending stress occurs when the top layer is under compression and the bottom layer is under tension. In between these layers, there is a neutral stretched layer that hasn’t been subjected to stress.
Unlike in other stresses, bending stress is not determined by simply dividing the stress by area. Therefore, to determine bending stress, we have to take the bending moment, vertical distance away from the neutral axis and moment of inertia around the neutral axis.
To calculate the bending moment of a point, you can multiply the force acting on the structure and the perpendicular distance to the point.
M = Fx
And the following equation is used to calculate the bending stress.
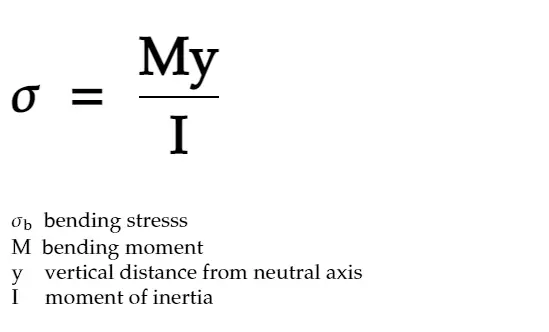
Torsional Stress
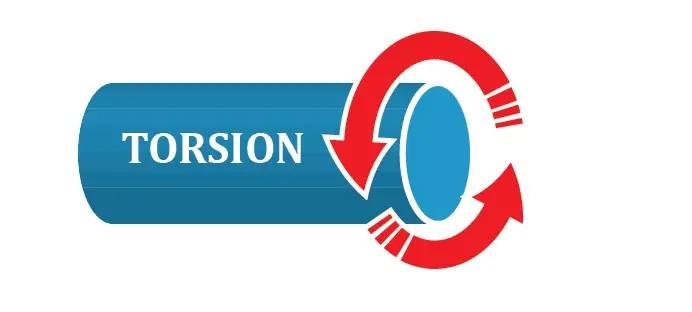
Torsional stress is shear stress caused due to twisting. In other words, it may be described as the angular deformation of a body.
Torsional stress is the hardest stress to calculate. To calculate the torsional stress, we have to build a relationship between torque and shear stress.
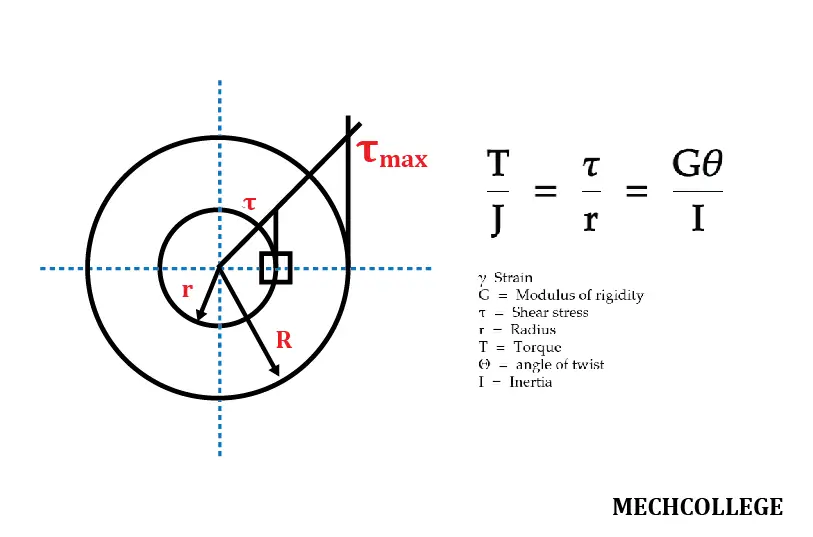
Conclusion
Stress analysis is one of the primary aspects that design engineers examine. Otherwise, the machine is more likely to fail. However, the majority of non-engineers, do not actually care about calculations. And they design the product with larger assumed values. However, from an economical standpoint, it’s not that effective.